新材料-中国制造2025详解(九)
九、 新材料
9.1 先进基础材料 先进基础材料是指具有优异性能、量大面广且“一材多用”
的新材料,主要包括钢铁、有色、石化、建材、轻工、纺织等基 础材料中的高端材料,对国民经济、国防军工建设起着基础支撑 和保障作用。
9.1.1 需求
基础材料产业是实体经济不可或缺的发展基础,我国百余种 基础材料产量已达世界第一,但大而不强,面临总体产能过剩、 产品结构不合理、高端应用领域尚不能完全实现自给等三大突出 问题,迫切需要发展高性能、差别化、功能化的先进基础材料, 推动基础材料产业的转型升级和可持续发展。
9.1.2 目标
到 2020 年,基础材料产业总体规模得到有效控制,产业结 构调整初见成效,先进基础材料总体实现自给,形成一定出口能 力。
到 2025 年,产业结构调整显著,基础材料产品结构实现升 级换代,国内市场占有率超过 90%。
9.1.3 发展重点
1.先进钢铁材料
(1)先进制造基础零部件用钢 突破先进装备用高性能轴承、齿轮、工模具、弹簧、紧固件等用钢的材料、设计、制造及应用评价系列关键技术,高效节能电机、高端发动机、高速铁路、高端精密机床、高档汽车等先进装备用关键零部件用钢铁材料国内自给率 2020 年达到 80%,2025 年力争全面自给,关键零部件寿命提高 1 倍以上。
(2)高性能海工钢
通过 690MPa 级低预热焊接特厚板及无缝管(100mm)以上、 420-460MPa 级可大线能量焊接厚板、R6 级大规格锚链钢的研发、 生产、应用技术和规范标准研究,实现工程化示范考核,满足我 国 400 英尺以上自升式平台、重型导管架平台以及新一代半潜式 平台对国产材料的迫切需求;高端海工钢的国内市场占有率从现 在的不足 50%提升到 90%以上,采购成本较进口材料降低 20%以 上。
(3)新型高强韧汽车钢
研发包括 Q& P、δ -TRIP、中锰钢、TWIP 及低 Mn-TWIP 钢等 在内的新型超高强韧汽车用钢,强塑积达到 20-50GPa%。
(4)高速、重载轨道交通用钢
350km/h 以上高断裂韧性、高疲劳性能车轮钢,30-40 吨轴 重重载货车车轮用钢,承载寿命 2-4 亿吨级快速重载铁路用钢 轨,新型热处理贝氏体钢轨(抗拉强度≥1400MPa,延伸率≥10%)。
(5)新一代功能复合化建筑用钢
厚度 100mm 以上、屈服强度 600-1000MPa、屈强比低于 0.8-0.85、600℃时的屈服强度高于室温强度指标的 2/3,弹性 模量高于室温时 75%以上。
(6)超大输量油气管线用钢X90/100 超高强管线钢,以及 33mm 以上厚度规格 X80 级别管线钢。
(7)轧制复合板 开发符合组坯工艺、高效焊接、在线固溶等轧制复合板关键技术、解决生产优质坯料厚度 500-900mm 的产出率低、能耗高技 术难点,开发系列复合板产品,满足化工、海水淡化、能源等特 种行业对材料的特殊要求。
(8)特种装备用超高强度不锈钢
开发屈服强度 1400-2200MPa、企业具有高抗应力浮士德高 强不锈钢系列品种,满足航空、深海钻探、油田化工、特种船舶 等行业。
2.先进有色金属材料
(1)高性能轻合金材料
研发 650MPa 级新型高强韧、低淬火敏感性、厚度 200mm 以 上铝合金预拉伸板;研制≥700℃高温钛合金和 1300MPa 以上高 强韧钛合金、直径≥Ф 450mm 超大规格棒材等。加工成材率提高 10%。
(2)功能元器件用有色金属关键配套材料
稀有稀贵及高纯金属在现有基础上纯度提高 1-2N,注重材 料的循环再生与高效利用,利用率提高 10%;开发 600mm 以上高 纯无氧铜压延铜箔等配套材料。
3.先进石化材料
(1)润滑油脂
注重基础油的开发与利用,加大对加氢基础油、GTL 基础油、可生物降解等高档基础油在内的燃机油和液压油、汽轮机油、润 滑脂等领域的应用;加大添加剂的开发与应用,针对新的环保法 规提出的低硫、低磷、低灰分、低毒性、生物可降解、长寿命等 特种性能要求的抗氧剂、粘度指数改进剂、清净分散剂、摩擦改 进剂等添加剂产品进行分子设计、开发与应用。实现在液压油、 工业齿轮油、透平油、润滑脂最常见工业润滑油脂的通用型产品 的自主知识产权配方开发;开发高性能长寿命空间润滑剂产品。
(2)高性能聚烯烃材料 突破高熔融指数聚丙烯、超高分子量聚乙烯、发泡聚丙烯、聚丁烯-1(PB)等工业化生产技术,实现规模应用。
(3)聚氨酯树脂 重点发展环保型聚氨脂材料如水性聚氨酯材料,加快发展脂肪族异氰酸酯等原料。
(4)氟硅树脂 重点发展聚偏氟乙烯、PET、其它氟树脂以及硅树脂、硅油 等。
(5)特种合成橡胶 重点发展异戊橡胶并配套发展异丁烯合成异戊二烯;发展硅橡胶、溶聚丁苯橡胶和稀土顺丁橡胶;发展卤化丁基、氢华丁腈 等具有特殊性能的橡胶等。
(6)生物基合成材料 重点突破生物基橡胶合成技术,生物基芳烃合成技术,生物基尼龙制备关键技术,新型生物基增塑剂合成及应用关键技术,生物基聚氨酯制备关键技术,生物基聚酯制备关键技术,生物法 制备基础化工原料关键基础技术等。
4.先进建筑材料
(1)极端环境下重大工程用水泥基材料 满足水电工程的冲刷磨损、气蚀破坏混凝土,非贯穿裂缝、渗漏修补水泥基材料;满足海洋工程用高抗侵蚀低碳水泥基胶凝 材料,超高强、高韧低碳水泥基复合材料;满足超低温海洋油田 固井水泥制备技术,复杂地质环境下固井(高温、酸性气体侵蚀) 自修复水泥基材料;满足轨道交通用道桥混凝土结构超快速修复 水泥基材料。
(2)节能绿色结构-功能一体化建筑材料 固体废弃物在产品中利用率≥70%,产品抗压强度≥20MPa,抗折强度≥7MPa,面密度≤50kg/m2,并集保温、隔热、防水、 防火、装饰于一体的结构-功能一体化建筑材料。
(3)环境友好型非金属矿物功能材料 开发渗透系数≤5.0×10-11m/s 的防渗材料,难溶钾转化率≥80% 及 生 防 菌 ≥ 2.5 × 1013 个 /kg 的 土 壤 修 复 剂 , 悬 浮 物 SS< 30mg/L、COD< 100mg/L 的水处理剂,指定摩擦系数 0.4±0.06 的摩擦材料,导热系数≤0.05W/m?K 的保温材料,氧指数≥35% 的阻燃剂及高强石膏、高效冶金保护渣、高端石墨制品、高效催 化剂、助滤剂、缓控释药物和化肥、高性能聚合物等典型新材料。
5.先进轻工材料
(1)生物基轻工材料
重点发展聚乳酸(PLA)、聚丁二酸丁二酯(PBS)、聚对苯二 甲酸二元醇酯(PET、PTT)、聚羟基烷酸(PHA)、聚酰胺(PA) 等产品。PLA 关键单体 L-乳酸和 D-乳酸的光学纯度达 99.9%以上, 成本下降 20%;PBS 关键单体生物基丁二酸、1,4-丁二醇提高生 物转化率达 5-10%;PTT 关键单体 1,3-丙二醇以木薯淀粉、甘 油等非粮原料发酵生产,PTT 纤维聚合纺丝实现产业化;PA 关键 单体戊二胺硫酸盐成品纯度高于 99%,成本下降 20%。
(2)工业生物催化剂 重点发展脂肪酶、脂肪氧合酶、葡萄糖氧化酶、天冬酰胺酶、氨基甲酸乙酯降解酶等食品工业用酶;漆酶、碱性木聚糖酶、角 蛋白酶、胰蛋白酶、PVA 降解酶等轻工纺织用酶;脂肪酶、氨基 酸脱氨酶、天然产物糖基化酶和透明质酸酶等生物有机合成用 酶。关键产品酶活在现有基础上提升 100-300%;极端条件下(温 度、PH)酶活达到或超过国外同类产品。
(3)特种工程塑料 重点发展基于热塑性聚酰亚胺(PI)工程塑料树脂、杂萘联苯型聚醚砜酮共聚树脂(PPESK)、高端氟塑料的加工成型的特种 纤维、过滤材料、耐高温功能膜、高性能树脂基复合材料、耐高 温绝缘材料、耐高温功能涂料、耐高温特种胶粘剂。热塑性聚酰 亚胺工程塑料树脂,粘度 0.38dL/g,Tg=230-310℃,Td5%> 500℃, 拉伸强度> 100MPa,弯曲强度> 150MP,成本< 15 万/吨;杂萘联苯 型聚醚砜酮共聚树脂,Tg=263-305℃,拉伸强度 90-122MPa,拉伸模量 2.4-3.8GPa,体积电阻率 3.8-4.8×1016Ω ·cm,成本降低到 PEEK 的 50-70%。高端氟塑料主要性能指标:超纯氟塑料 制品:PTFE 固体表现密度 SSG≤2.147g/cm3,PTFE 树脂拉伸强度>28MPa,伸长率>350%,绝缘强度>3.5KV/mil。满足 SEMI 标 准中 C12 的要求;耐高低温氟材料功能膜、特种氟纤维及过滤产 品:满足高端环保要求,PTFE 树脂要求压缩比>3000,拉伸强 度>28MPa,伸长率>360%;油气及化工流体输送用泵、阀门及 管 道 用 PVDF 树 脂 要 求 密 度 1.75-1.77g/cm3, 熔 指 0.5-2.0g/10min,熔点 156-165℃,热分解温度≥390℃,含水率≤0.10%,玻璃化温度≤-35℃,脆化温度≤-62℃。 6.先进纺织材料
(1)高端产业用纺织品
2020 年实现可吸收缝合线、血液透析材料的自主产业化, 部分替代国外进口产品;满足热、生化、静电、辐射等功能防护 要求;高温过滤、水过滤产品性能满足各应用领域要求;土工材 料满足复杂地质环境施工要求。2025 年,满足多功能复合防护 要求,同时实现轻质、舒适和部分智能化,过滤产品寿命和稳定性进一步提升,实现低成本应用和智能化监测预警等功能结合。
(2)功能纺织新材料
2020 年,阻燃极限氧指数﹥32,无熔滴,滴水扩散时间﹤1s,能耗降低 20%。2025 年高端产品基本实现自给。
(3)生物基化学纤维
2020 年 PTT 纤维原料 1,3-丙二醇纯度大于 99.5%,成本控制在 1.5 万元/吨以下;聚乳酸耐热温度≥110℃,单体纯度≥99.9%,PLA 纤维断裂强度大于 3.5g/d,断裂伸长 30%-35%。2025 年 PLA 纤维生产成本接近 PET 生产成本。
9.1.4 战略支撑与保障条件
1.设立重大专项资金,重点支持产学研用创新联盟,加强新 材料研发与先进制造紧密结合,开发和突破一批面向各基础材料 行业转型升级的共性关键技术和重大应用技术。
2.对产业发展具有带动性或突出贡献的骨干企业或重大项 目给予财政后补贴强力支持,关键人员给予重奖。
3.加强基础共性标准、关键技术标准和重点应用标准的研究 制定;积极参与国际标准化工作。
4.建立第三方检测评价等公共服务平台、新材料技术成熟度 评价体系和新材料产品认定体系,构建国家基础新材料数据库。
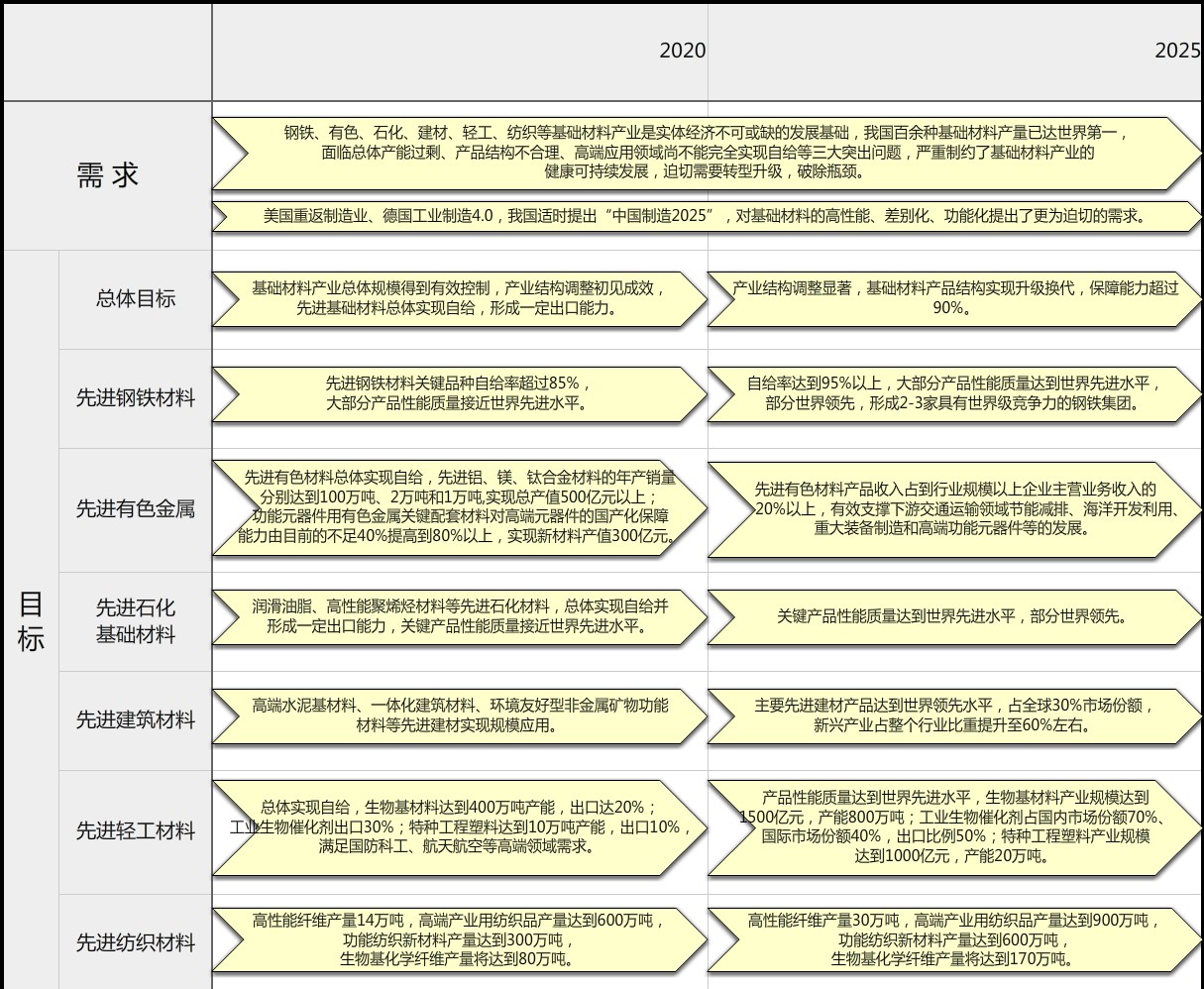
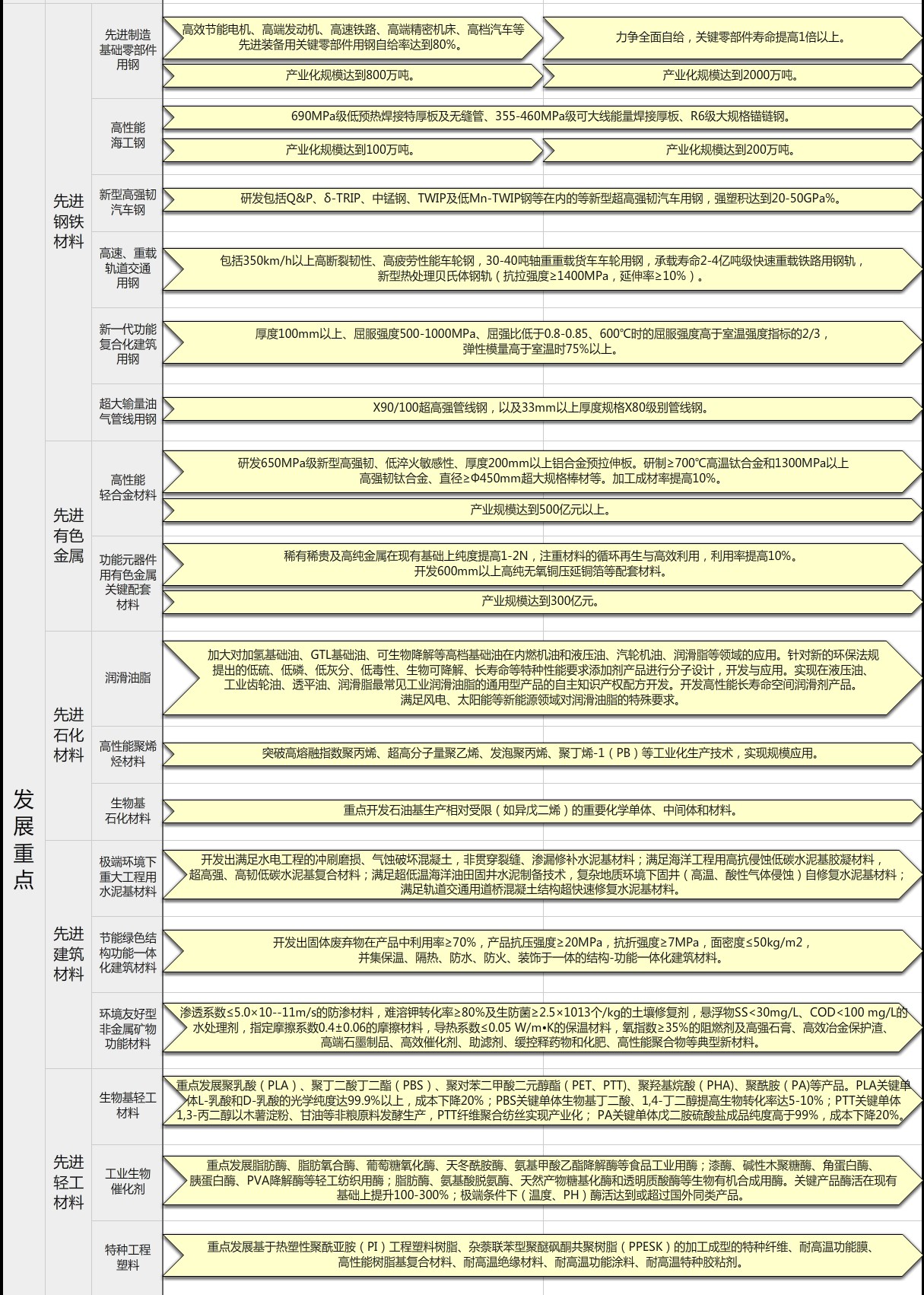
9.2 关键战略材料
关键战略材料主要包括高端装备用特种合金、高性能分离膜 材料、高性能纤维及其复合材料、新型能源材料、电子陶瓷和人 工晶体、生物医用材料、稀土功能材料、先进半导体材料、新型 显示材料等高性能新材料,是实现战略新兴产业创新驱动发展战 略的重要物质基础。
9.2.1 需求
关键战略材料,是支撑和保障海洋工程、轨道交通、舰船车 辆、核电、航空发动机、航天装备等领域高端应用的关键核心材 料,也是实施智能制造、新能源、电动汽车、智能电网、环境治 理、医疗卫生、新一代信息技术和国防尖端技术等重大战略需要 的关键保障材料,目前,在国民经济需求的百余种关键材料中, 约三分之一国内完全空白,约一半性能稳定性较差,部分产品受 到国外严密控制,突破受制于人的关键战略材料,具有十分重要 的战略意义。
9.2.2 目标
到 2020 年,实现 30 种以上关键战略材料产业化及应用示范。 有效解决新一代信息技术、高端装备制造业等战略性新兴产业发 展急需,关键战略材料国内市场占有率超过 70%;初步形成上下 游协同的战略新材料创新、应用示范体系和公共服务科技条件平 台。
到 2025 年,高端制造业重点领域所需战略材料制约问题基 本解决,关键战略材料国内市场占有率超过 85%。部分产品进入国际供应体系,关键品种填补国内空白,实现自主知识产权体系。
9.2.3 发展重点
1.高端装备用特种合金
(1)先进变形、粉末、单晶高温合金 突破高温合金的低成本规模化生产技术;突破第四代粉末、单晶、点阵材料等新一代高温合金关键技术;打通先进高温合金 制备工艺流程。国产高代次涡轮盘和单晶叶片等高温合金产品形 成稳定供应能力,满足航空发动机与燃气轮机重大专项对高温合 金材料的需求。
(2)特种耐蚀钢及 700℃超超临界电站用耐热合金 研发耐大气、海洋、油气、高温、复杂应力状态等环境腐蚀的钢铁材料,全面提高我国耐蚀钢产业技术水平,典型钢种耐蚀 性能提高 1 倍以上,并构建起自主知识产权的耐蚀钢材料体系。 开发超级镍基合金、锅炉管材、高中压转子锻件,蒸汽发生器传 热管、主泵电机材料、安全壳、专用焊接材料等,支撑 700℃超 超临界电站示范工程建设。
(3)特种铝镁钛合金 开发特种规格铝、镁、钛合金材料制备及精密成形工艺与控制、服役性能评价等技术,研发 650MPa 级新型高强韧、低淬火 敏感性、厚度 200mm 以上铝合金预拉伸板;500MPa 级高强韧、 耐热 250℃以上镁合金以及抗疲劳、抗蠕变、耐冲击、高塑性等 系列镁合金;研制≥700℃高温钛合金和 1300MPa 以上高强韧钛 合金、直径≥Ф 450mm 超大规格棒材等。加工成材率提高 10%。
2.高性能分离膜材料
(1)海水淡化反渗透膜产品
脱盐率大于 99.8%,水通量提高 30%,海水淡化工程达到 200 万吨/日,装备国产化率大于 80%。
(2)陶瓷膜产品
装填密度超过 300m2/m3,成本下降 20%,需求量达到 20 万 m2,突破低温共烧结技术,形成气升式膜分离装备,能耗下降 30%。
(3)离子交换膜产品
膜性能提高 20%,氯碱工业应用超过 1000 万吨规模,突破 全膜法氯碱生产新技术和成套装置。
(4)中空纤维膜产品 在自来水生产、污水处理等领域应用超过 1000 万吨/日,膜
面积超过 2000 万 m2。
(5)渗透汽化膜产品
渗透通量提高 20%,膜面积达到 10 万 m2,突破大型膜组器 和膜集成应用技术,推广应用规模超过百万吨溶剂脱水和回收, 节能 30%以上。
3.高性能纤维及复合材料
(1)高性能碳纤维及其复合材料
2020 年国产高强碳纤维及其复合材料技术成熟度达到 9 级, 实现在汽车、高技术轮船等领域的规模应用;2025 年,国产高 强中模、高模高强碳纤维及其复合材料技术成熟度达到 9 级;力争在 2025 年前,结合国产大飞机的研发进程,航空用碳纤维复合材料部分关键部件取得 CAAC/FAA/EASA 等适航认证。碳纤维(T800 级)拉伸强度≥5.8GPa,CV≤4%,拉伸模量 294GPa,CV≤4%。
(2)高性能对位芳纶纤维及其复合材料
2025 年国产对位芳纶纤维及其复合材料技术成熟度达到 9 级。
建立统一标准的高性能纤维材料技术体系,攻克系列化高性 能纤维高效制备产业化技术,开展与国产高性能纤维相匹配的复 合材料基体材料、设计技术、成型工艺、性能表征、应用验证及 回收再利用等研究,确保重大装备需求。对位芳纶断裂强度 20-22cN/dtex,断裂伸长率 3-4%;聚酰亚胺纤维单丝纤度为 2.0dTex,强度>4cN/dTex,极限氧指数为 38%。
(3)其他高性能纤维及其复合材料 重点发展金属基、陶瓷基先进复合材料、构件及相关工艺装备;聚酰亚胺纤维单丝纤度为 2.0dTex,强度>4cN/dTex,极限 氧指数为 38%;超高分子量聚乙烯纤维、玄武岩纤维、聚苯硫醚 纤维、高强度高模量聚乙烯醇缩甲醛纤维、聚四氟乙烯纤维、碳 化硅纤维等重要品种;开发高性能 PBO 纤维,拉伸强度 5.8GPa, 模量 270GPa,极限氧指数为 68%。
4. 新型能源材料
(1)太阳能电池 晶硅电池效率≥25%,硅基薄膜电池效率≥15%,光伏系统上网电价≤0.5 元/kWh;有机太阳能电池能量转换效率≥20%;染料敏化太阳能电池光电转换效率≥15%。
(2)锂电池
能量型锂电池比能量≥300Wh/kg,功率型锂电池比功率≥ 4000W/kg;动力电池≤1.5 元/Wh,储能电池≤1.0 元/Wh,材料 及电池生产设备全部实现国产化。
(3)燃料电池
燃料电池系统≤0.3 万元/kW,膜电极成本≤50 元/kW,高温 复合膜成本≤0.3 万元/m2。
5.新一代生物医用材料
(1)再生医学产品
研制出 5-10 种应用于骨、皮肤、神经等组织再生修复的生物活性材料,高端再生医学产品年产规模 50 亿元。
(2)功能性植/介入产品
开发出 5-10 项应用于心血管、人工关节、种植牙、视觉恢 复等临床治疗的生物医用材料,高端功能性植/介入产品年产规 模 30 亿元。
(3)医用原材料 实现重要原材料的国产化,支撑量大面广的医用耗材、渗透膜、可降解器械等产品,实现年产规模 30 亿元。 6.电子陶瓷和人工晶体
(1)电子陶瓷
重点开发介电常数高于 1 万且介电损耗低于 0.1 的高 k 电介质陶瓷。
(2)人工晶体 开发大尺寸、高质量、低成本的人工晶体材料;突破大尺寸非线性晶体(中远红外、紫外、深紫外)、高光产额闪烁晶体, 低缺陷蓝宝石等产业化关键技术,并规模应用。
7.稀土功能材料
(1)稀土磁性材料
烧结磁体综合性能(磁能积(MGOe)+矫顽力(kOe))80;Ce 含量占稀土总量的 40%时磁能积> 40MGOe。
(2)稀土光功能材料
白光 LED 荧 光 粉 应 用 器 件 光 效 > 200lm/W ,满足广色域 (> 100%NTSC)显示屏应用需求。
(3)稀土催化材料 汽油烯烃和硫含量、机动车催化剂及器件满足国Ⅵ排放标准。
(4)稀土储氢材料 开发高能量密度、低成本的新型动力和储能电池材料;形成
电池材料及制品的自动化控制、工业生产、成套装备能力与测试 评价平台。
(5)超纯稀土材料
稀土氧化物纯度 6.5N,稀土金属纯度 4.5N。
重点突破新型稀土材料成分设计与高通量制备技术、稀土功能材料微观组织可控制备技术、稀土荧光粉高温高压合成及表面包覆技术、稀土高效分离提纯技术等共性关键技术。
8.先进半导体材料
(1)第三代半导体单晶衬底
6-8 英寸 SiC、4-6 英寸 GaN、2-3 英寸 AlN 单晶衬底制备技 术;可生产大尺寸、高质量第三代半导体单晶衬底的国产化装备。
(2)第三代半导体光电子器件、模块及应用
200 lm/W 以上光效的 LED 外延和芯片制备技术;50mW 以上 AlGaN 基紫外 LED。
(3)第三代半导体电力电子器件、模块及应用
15kV 以上 SiC 电力电子器件制备关键技术;高质量、低成 本 GaN 电力电子器件的设计与制备;在高压电网、高速轨道交通、 消费类电子产品、新能源汽车、新一代通用电源等领域的应用。
(4)第三代半导体射频器件、模块及应用
100Mhz 以上 GaN 基 HEMT 微波射频器件和模块;5G 移动通信 和卫星通信领域中的应用。
(5)450mm 大直径硅片
450mm 硅材料制备关键技术;年产 5 万片以上 450mm 硅片的 引导线。
9.显示材料
(1)印刷显示
2020 年,60 英寸级、4K2K 高分辨率印刷 OLED 显示屏,2025 年 100 英寸级、8K4K 超高分辨率印刷 AMOLED 显示屏。
(2)柔性显示
2020 年,300PPI 分辨率中小尺寸柔性 AMOLED 显示屏,可弯 曲直径< 1cm,2025 年,100 英寸级、可卷绕式 8K4K 柔性显示, 中小尺寸可折叠显示屏。
(3)激光显示
2020 年,100 英寸级高清激光家庭影院,色域空间达到160%NTSC,2025 年,200 英寸超高清激光显示产品,色域空间达 到 200%NTSC。
9.2.4 战略支撑和保障
1.设立关键战略材料专项计划;集中力量突破先进核心工程 化工艺技术制约,提升关键战略材料产业共性工艺技术创新水 平。
2.在重点领域创建一批由新材料生产企业、重点用户和科研 院所共同组建的国家级新材料产业联合创新中心,开展上下游协 同创新。鼓励建立产学研创新联盟,开展关键战略材料开发及应 用。
3.加强关键战略材料标准及应用标准的研究制订。
4.深入推动军民融合发展,实现新材料技术双向转移。
5.建立新材料“首批次”应用风险补偿机制,完善保险、财 税等综合配套政策,加强对新材料初期市场的培育和支持力度。 开展新材料技术成熟度评价和认定。
9.3 前沿新材料
革命性新材料的发明、应用一直引领着全球的技术革新,推 动着高新技术制造业的转型升级,同时催生了诸多新兴产业。在 发挥前沿新材料引领产业发展方面,我国的自主创新能力严重不 足,迫切需要在 3D 打印材料、超导材料、智能仿生与超材料、 石墨烯等新材料前沿方向加大创新力度,加快布局自主知识产 权,抢占发展先机和战略制高点。
9.3.1 需求
未来 10 年,为满足航空航天、生物医疗、汽车摩配、消费 电子等领域对个性化、定制化复杂形状金属制品的需求,3D 打印金属粉末需求量将年均增长 30%,到 2020 年需求量达 800 吨,到 2025 年达 2000 吨。我国在智能电网、大科学装置方面对超导材料的需求持续增长,到 2020 年需求量将达到 100 亿元,到 2025年达到 150 亿元。智能仿生与超材料是智能制造、智能传感的核 心材料,实现规模化制造及应用极为迫切,预计将以 40%的年复 合增长率快速发展,到 2020 年,其市场规模将达近 650 亿美元。 石墨烯材料集多种优异性能于一体,是主导未来高科技竞争的超 级材料,广泛应用于电子信息、新能源、航空航天以及柔性电子 等领域,可极大推动相关产业的快速发展和升级换代,市场前景 巨大,有望催生千亿元规模产业。
9.3.2 目标
到 2020 年,积累一批前沿新材料核心技术专利,部分产品 实现量产,在关键领域实现应用示范。
到 2025 年,实现前沿新材料技术、标准、专利等有效布局;
前沿新材料取得重要突破并实现规模化应用,部分领域达到世界 领先水平。
9.3.3 发展重点
1. 3D 打印用材料
(1)低成本钛合金粉末
满足航空航天 3D 打印复杂零部件用粉要求,低成本钛合金 粉末成本相比现有同等钛合金粉末降低 50~60%。
(2)铁基合金粉末
利用 3D 打印工艺致密化后的金属制品,其物理性能与相同 合金成分的精铸制品相当。
(3)高温合金粉末 开发金属粉末的致密化技术,建立制品的评价标准体系。
(4)其它 3D 打印特种材料
突破适用于 3D 打印材料的产业化制备技术,建立相关材料 产品标准体系。
2.超导材料
(1)强磁场用高性能超导线材 掌握高性能超导线材结构设计及批量化加工控制技术。
(2)低成本千米级 YBCO 涂层导体掌握涂层导体织构化基带、功能层沉积技术和 MOCVD、PLD 制造装备。
(3)高电压等级超导限流器等应用产品掌握高电压等级超导限流器等应用产品的电磁设计、超高压绝缘、装配结构与挂网运行等关键技术。 整体突破高性能低成本超导线材集束拉拔塑形加工技术、大型高效长寿命制冷机技术和低漏热低温容器制备技术、面向不同 波段和频率的超导应用产品制备技术。
3.智能仿生与超材料
(1)可控超材料与装备 实现特定频段内电磁波从吸波与透波的可控转换,或者将特
定频段内的吸波或透波转换为辐射电磁波。
(2)仿生生物粘附调控与分离材料 实现长效抗海洋生物粘附(3 年,低于 5%),环境无毒害;
实现高效的粘附调控富集分离 99%以上;获得 2-3 种长效仿生抗 海洋生物粘附的涂层材料及仿生高效分离技术与装备。
(3)柔性智能材料与可穿戴设备 实现柔性仿生智能材料“卷对卷”的生产,实现电磁可调、
智能传感、0-360 度任意弯曲、与人体兼容。 整体突破仿生生物粘附调控与分离材料的大面积制备与涂
层黏合技术;智能材料的柔性化、大面积的制备和生物兼容技术; 具有智能化和仿生特性的自适应可控式超材料的联合设计技术。
4.石墨烯材料
(1)电动汽车锂电池用石墨烯基电极材料 较现有材料充电时间缩短 1 倍以上,续航里程提高 1 倍以上。
(2)海洋工程等用石墨烯基防腐蚀涂料较传统防腐蚀涂料寿命提高 1 倍以上。
(3)柔性电子用石墨烯薄膜性价比超过 ITO,且具有优异柔性,可广泛应用于柔性电子 领域。
(4)光/电领域用石墨烯基高性能热界面材料 石墨烯基散热材料较现有产品性能提高 2 倍以上。 整体突破石墨烯的规模制备技术,石墨烯粉体的分散技术,石墨烯基电极材料的复合技术。 9.3.4 战略支撑和保障
1.设立前沿新材料专项计划和专项资金。
2.集中力量建立若干国家级前沿新材料创新中心。
3.加强前沿新材料标准及应用标准的研究制订。
4.优先支持前沿新材料的示范应用。
5.建立产需对接长效机制,建设若干前沿新材料产业基地。